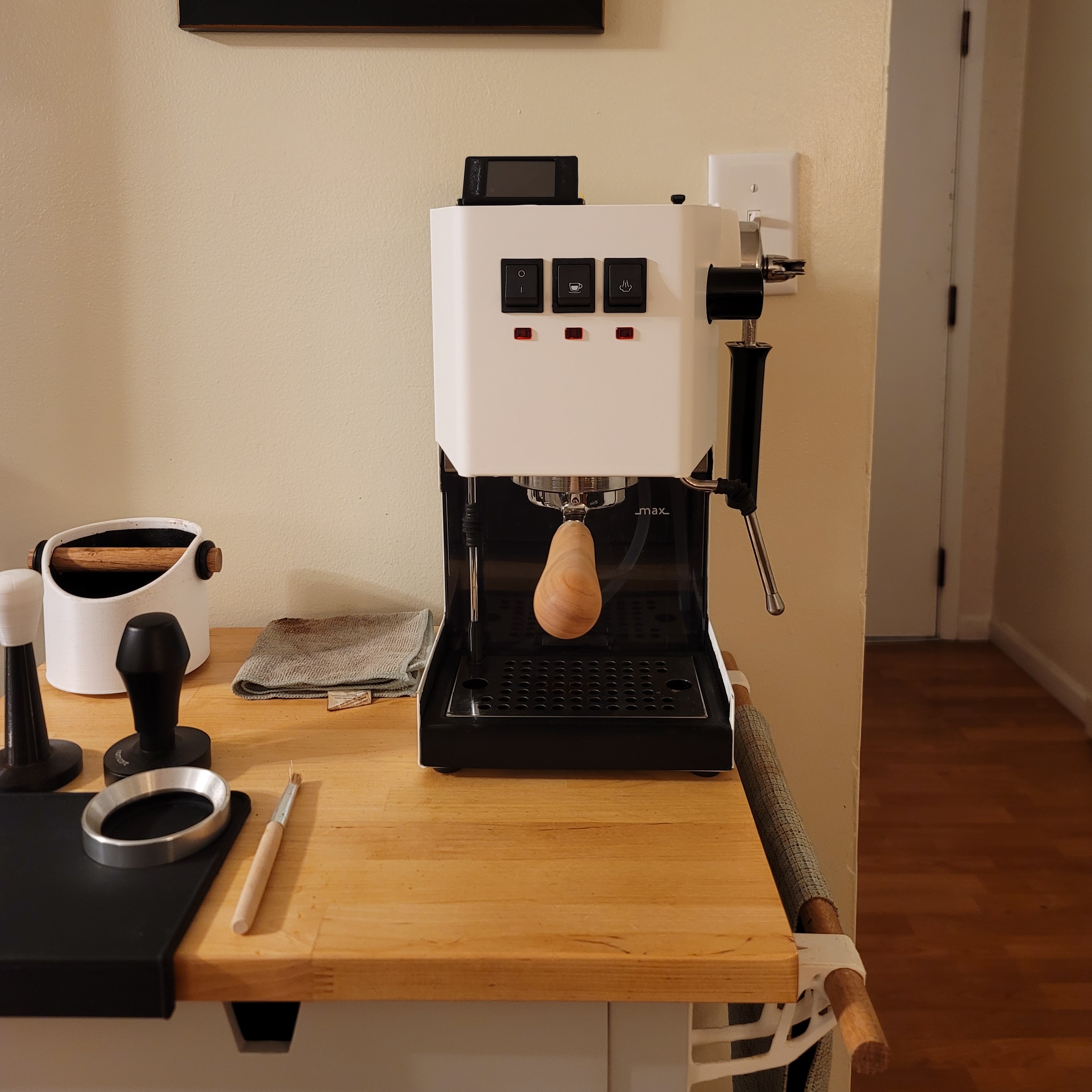
Gaggiuino and Topology Optimization
I've always seen forged carbon parts and enjoyed how they looked. I then stumbled upon an EasyComposites video showing how to use a 3D-printed mold to make forged carbon fiber parts and I knew I had to make something. Once I got my car I thought this would be the perfect project to learn how to fabricate forged carbon fiber parts.
To begin the process I have to have a 3d model of a shift knob, to then make a mold around it. So, I had to design the shift knob I wanted. I knew I wanted the cylindrical style, so I started with a very basic design. I used very rough dimensions from my holding different poles to get the overall shape, and then I added a chamfer to the top and a slight taper on the bottom. Once I got that design done, I then printed out a model, using vase mode to reduce the amount of filament used, to get an overall idea of how it would feel. I then found out I go it too short, so I adjusted that dimension. I then went with this process two more times until I settled on a shape. Once the overall geometry was decided I then printed out one with the normal print settings, not hollow, to make sure the bottom hole was the correct dimension and to confirm that it was the correct design. A lineup of all the versions can be seen in the picture below.
Once I finished the design of the shift knob I just used the 3d geometry as the negative of the mold. From there I had a block with a negative of the shift knob, which isn't that useful. So, to begin with, I decided to split the mold into three pieces, I chose this because it allows for easier removal of the part and a forged carbon fiber part needs a plunger. The plunger of the mold is needed as forged carbon fiber parts take their shape by the pressure of pressing the resin and chopped fibers together. From there I needed a method to keep the mold parts parallel to each other so I added holes in the corners to allow for long bolts to clamp the mold. Lastly, I added a chamfer to the parting lines of the mold to aid in the removal of the part.
When the design of the mold was finished I printed them out using PTEG and 90% infill, I did this because I needed the part to be very strong to withstand the high clamping forces that will be applied to it. I then just followed the processes laid out in the EasyComposites video. Since I designed the part in SolidWorks getting the volume of the part was easy, and that is needed because that's how one knows how much carbon fiber to resin is needed. I used a bolt that I found that matched the diameter of the large hole on the bottom as a placeholder to minimize the amount of post-processing needed.
When the part was done curing, it looked like the below picture. As you can see there is a lot of post-processing needed. To clean it up I used the learning factory, a makerspace at Penn State, to sand down the flashing and make the part smooth. I also made the hold on the bottom to the correct diameter, using the drill press. I then needed to make a treaded insert so the shift knob can screw into the car's transmission. To do this I used an aluminum stock and the lathe. When that was done I then used some JB-weld to adhere it to the inside of the shift knob.